Utvärdering av tillverkningsmetoder för svarvbommar
Full text
(2) Sammanfattning På dagens konkurrenskraftiga marknad har industriföretag fått allt svårare att uppnå lönsamhet genom höga priser på tillverkade produkter. Lönsamhet måste istället uppnås genom låga tillverkningskostnader, god produktkvalité samt korta genomloppstider. Ett av företagen på den konkurrensutsatta marknaden är Sandvik Coromant i Gimo, tillverkare av verktyg och skär för skärande bearbetning. Detta examensarbete utreder tillverkning av svarvbommar vid avdelningen GVH4 på Sandvik Coromant i Gimo. Avdelningen tillverkar i dagsläget sina produkter med två olika tillverkningsmetoder, en där stålämnen härdas före bearbetning och en där härdning utförs efter bearbetning. Tillverkningen sker i ett flertal olika delprocesser som påverkas olika beroende av vilken metod som används. Med verktyget värdeflödesanalys har produktionsledtider, fakta om delprocesser, materialflöden och informationsflöden kartlagts för de två tillverkningsmetoderna. Genom studier av hur cykeltider vid tillverkning i olika delprocesser påverkas av metodval samt genom ekonomiska kalkyler med ett aktivitetsbaserat synsätt, har sedan en analys gjorts av vilken metod som bör föredras ur ett produktionsekonomsikt perspektiv. För att införskaffa information har intervjuer gjorts med personal på berörda avdelningar. Observationer av materialflöden och mellanlager gjordes samtidigt som produkter i arbete beräknades. Cykeltider har insamlats genom egna mätningar. Fakta för ekonomiska kalkyler har tagits från företagets ekonomiska uppföljning. Där det i vissa fall inte funnits rätt uppföljning, har egna utredningar gjorts. Resultatet av värdeflödesanalysen blev en beskrivande karta över material- och informationsflödet i nuläget. Utifrån värdeflödesanalysen kunde även skillnaderna i produktionsledtider mellan de två tillverkningsmetoderna tydligt åskådliggöras. Mätningar av cykeltider visade även på intressanta fakta gällande den värdehöjande tiden. Mätningar av cykeltider och de ekonomiska kalkyler som gjorts visar att metoden där bearbetning utförs före härdning är att föredra ur ett ekonomiskt perspektiv. De totala kostnaderna för avdelningen har i utredningen visats bli cirka 6 % lägre vid enbart tillverkning med denna metod. Utredningen har även visat att metoden där bearbetning utförs före härdning är att föredra vid en eventuell volymökning, då fler produkter kan tillverkas innan nyinvesteringar krävs. En sammanställning av kvalitetsaspekter som kan påverkas vid val av tillverkningsmetod har även gjorts, innehållande förslag på vad som bör utredas ytterligare..
(3) Abstract On today’s competitive market, it is difficult to achieve profitability trough high prices on manufactured products. Profitability must be obtained through low manufacturing costs, high quality and short lead times. One of the companies on the market is Sandvik Coromant, manufacturer of tools and chips for metal cutting. This master thesis investigates the methods of manufacturing for boring bars at the manufacturing unit GVH4 at Sandvik Coromant in Gimo, Sweden. Currently the boring bars are manufactured with two different methods, one where the iron bar is hardened and annealed before further processing and one where the hardening and annealing is executed after most of the processing. The location of the hardening and annealing in the manufacturing process will affect the different manufacturing steps and also the material flow in the factory. With a value-flow analysis, the differences in material flow of the two manufacturing methods have been analysed. The valueflow analysis resulted in a mapping of the production lead-times, facts about the manufacturing steps, material flow and information flow. Trough a study of how the differences in cycle-times in the manufacturing steps are affected by the choice of manufacturing method and by economic calculations with an activity-based viewpoint, an analysis has been made to determine the method of choice. To obtain information interviews have been carried out with the personnel at the concerned departments. Observations of the flow of material and buffer stocks were carried out, at the same time the amount of products in work were calculated. The necessary facts for the economical calculations have been collected from the companies’ economical follow-up. In some cases where the follow-up has been obscure the writers have been compelled to make there own calculations of the cost in these areas. The result of the value flow analysis became a descriptive map over the current material- and information flow. From this analysis it has been determined how the production led times varies between dependent on the choice of manufacturing method. In conclusion: there is no substantial difference in led times between the two methods with today’s production setup. Measurements of the cycle-times have shown interesting facts about the time for increasing value of the products in the production. The measurements of cycle-times and the activity analysis of the production, has resulted in an economical calculation showing that processing before hardening and annealing is preferable, from an economic point of view. The investigation has shown that difference in total cost choosing this method, is about 6 %. If future increase in production volume is expected, the investigation has also shown that the preferred method is the one where the hardening and annealing is executed after processing. This is because a greater amount of boring bars can be manufactured before costly investments in production equipment become necessary. Furthermore, during the investigation it has become increasingly evident that there are some limitations in today’s economical follow-up regarding analysis of where and why resources are consumed in the production. The structure of the accountancy has limitations when it comes to examining possible economic consequences followed by changes in the production..
(4) The gathered material about quality aspects has resulted in a listing of quality aspects that are of importance for the choice of manufacturing method. Some of the quality aspects indicate that the implementation of hardening and annealing before processing is impossible for some products; this is due to requirements concerning hardness of the product. Finally, suggestions of areas to be further investigated before choosing manufacturing method have been made..
(5) Förord Detta examensarbete har utförts som en avslutning på civilingenjörsprogrammet i maskinteknik med inriktning mot produktionsteknik vid Luleå tekniska universitet. Examensarbetet är utfört på Sandvik Coromant i Gimo under perioden september 2008 till januari 2009. I examensarbetet har två metoder för tillverkning av svarvbommar utretts ur ett produktionsekonomiskt perspektiv samt att värdeflödena för dessa två tillverkningsmetoder kartlagts. Projektet har varit både intressant och lärorikt och vi hoppas att företaget kommer att få nytta av vad som framkommit av arbetet. Vi vill tacka alla som vi under arbetets gång kommit i kontakt med. Först och främst vill vi tacka våra handledare Urban Eriksson och Johan Åsberg. Vidare vill vi tacka vår examinator på Luleå tekniska universitet, Torbjörn Ilar. Vi vill även tacka alla produktionstekniker, operatörer samt produktionsledare på de berörda avdelningarna för deras positiva och hjälpsamma bemötande. Gimo, januari 2009. _____________________ Emanuel Fors. ___________________ Tobias Ahlström.
(6) Innehållsförteckning 1. Inledning................................................................................................................................... 1 1.1 Bakgrund .......................................................................................................................... 1 1.2 Syfte & mål ...................................................................................................................... 2 1.3 Avgränsningar .................................................................................................................. 2 2 Företagsbeskrivning ................................................................................................................. 3 2.1 Sandvik ............................................................................................................................. 3 2.1.1 Sandvik Coromant Gimo .............................................................................................. 3 2.2 Svarvbommen ................................................................................................................... 4 3 Nulägesbeskrivning .................................................................................................................. 5 3.1 Produktionsupplägg .......................................................................................................... 5 3.1.1 Råmaterial .................................................................................................................... 6 3.1.2 Internlego ..................................................................................................................... 6 3.1.3 Materialhantering ......................................................................................................... 6 3.2 Delprocesser ..................................................................................................................... 7 3.2.1 Pipborrning (BKH) ....................................................................................................... 7 3.2.2 Svarvning komplett (SKPL) ......................................................................................... 7 3.2.3 Fräsning komplett (FKPL) ........................................................................................... 8 3.2.4 Slipning (SLR) ............................................................................................................. 9 3.2.5 Riktning av svarvbommar (RK) ................................................................................. 10 3.2.6 Härdning och anlöpning (HÄ+ANL) ......................................................................... 10 3.2.7 Ytbehandling och montering av logotyp (JET+KLISKY) ......................................... 11 3.2.8 Montering och avsyning (M+ASY) ........................................................................... 11 3.3 Informationsflöde ........................................................................................................... 11 3.3.1 Orderhantering ........................................................................................................... 11 3.3.2 Orderstart .................................................................................................................... 12 3.3.3 Produktionen .............................................................................................................. 12 4 Teoretisk referensram ............................................................................................................. 13 4.1 Produktionsekonomi....................................................................................................... 13 4.1.1 Produktkostnad ........................................................................................................... 13 4.1.2 Produktionskvalité ...................................................................................................... 14 4.1.3 Bearbetningskostnad .................................................................................................. 14 4.1.4 Maskinutnyttjandegrad ............................................................................................... 15 4.2 Produktkalkylering ......................................................................................................... 16 4.2.1 Kalkylernas förutsättningar ........................................................................................ 16 4.2.2 Marknadsfaktorer ....................................................................................................... 16 4.2.3 Teknologins förändring .............................................................................................. 16 4.2.4 Produktkalkylering idag ............................................................................................. 17 4.3 Påläggskalkylering (traditionell kalkyl) ......................................................................... 17 4.4 Kalkylen och kostnadsstrukturen ................................................................................... 18 4.5 Aktivitetsbaserad kalkylering ......................................................................................... 19 4.5.1 Bakgrund till ABC-kalkylen ...................................................................................... 19 4.5.2 Grunden i den aktivitetsbaserade kalkylen ................................................................. 20 4.5.3 Aktiviteter................................................................................................................... 20 4.5.4 Aktivitetshierarki ........................................................................................................ 21.
(7) 4.5.5 Identifiering av aktiviteter .......................................................................................... 22 4.5.6 Resurser till aktiviteter (resursdrivare) ....................................................................... 22 4.5.7 Produkters förbrukning av aktiviteter......................................................................... 23 4.5.8 Sysselsättningsgrad och kapacitet .............................................................................. 24 4.6 Värdeflödesanalys (VFA) .............................................................................................. 24 4.6.1 Förutsättningar för en värdeflödesanalys ................................................................... 25 4.6.2 Tillvägagångssätt ........................................................................................................ 26 4.6.3 Kartläggning av nuvarande tillstånd .......................................................................... 26 4.6.4 Kartläggning av ett framtida tillstånd......................................................................... 27 5 Metod ..................................................................................................................................... 29 5.1 Kalkylering ..................................................................................................................... 29 5.2 Flödeskartläggning ......................................................................................................... 30 5.3 Tillvägagångssätt vid mätning av operationstider .......................................................... 30 5.3.1 FKPL .......................................................................................................................... 30 5.3.2 SKPL .......................................................................................................................... 31 5.3.3 SLR ............................................................................................................................. 31 5.3.4 RK .............................................................................................................................. 31 5.3.5 BKH ........................................................................................................................... 31 6 Resultat ................................................................................................................................... 32 6.1 Värdeflödesanalys (VFA) .............................................................................................. 32 6.2 Aktiviteter....................................................................................................................... 33 6.2.1 Aktiviteter i SKPL ...................................................................................................... 33 6.2.2 Aktiviteter i FKPL ...................................................................................................... 35 6.2.3 Aktiviteter i SLR ........................................................................................................ 36 6.2.4 Aktiviteter i RK .......................................................................................................... 36 6.2.5 Aktiviteter i BKH, M+ASY ....................................................................................... 36 6.2.6 Internlegoaktiviteter, kostnadsfördelning................................................................... 37 6.3 Resurser .......................................................................................................................... 37 6.4 Undersökning av resurskostnader från ekonomisk uppföljning GVH4 ......................... 37 6.5 Kartläggning av resurskostnader .................................................................................... 38 6.5.1 Operatörskostnad ........................................................................................................ 39 6.5.2 Verktygskostnad ......................................................................................................... 40 6.5.3 Avskrivningar ............................................................................................................. 41 6.5.4 Underhåll .................................................................................................................... 42 6.5.5 Lokalyta ...................................................................................................................... 43 6.5.6 Övriga resurser ........................................................................................................... 43 6.6 Förändring av tillverkningstid och resurskostnader ....................................................... 43 6.6.1 FKPL .......................................................................................................................... 44 6.6.2 SKPL .......................................................................................................................... 47 6.6.3 SLR ............................................................................................................................. 49 6.6.4 RK .............................................................................................................................. 51 6.7 Totala resurskostnaders förändring vid val av en tillverkningsmetod ........................... 52 6.8 Kvalitetsaspekter och Kvalitetsbriskostnader ................................................................ 53 6.8.1 Hårdhet ....................................................................................................................... 53 6.8.2 Formförändringar i härdning och anlöpning .............................................................. 54 6.8.3 Kassationer ................................................................................................................. 54 7 Slutsatser och rekommendationer .......................................................................................... 55.
(8) 7.1 Ekonomisk uppföljning .................................................................................................. 55 7.2 Utvärdering av formförändringar pga härdning, anlöpning och riktning....................... 55 7.3 Krav på hårdhet i plattläge ............................................................................................. 56 7.4 Förslag på fortsatt arbete ................................................................................................ 56 8 Diskussion .............................................................................................................................. 58 9 Referenser............................................................................................................................... 59 Bilaga A.1 .................................................................................................................................. 60 Bilaga A.2 .................................................................................................................................. 61 Bilaga A.3 .................................................................................................................................. 62 Bilaga A.4 .................................................................................................................................. 63 Bilaga B.1 .................................................................................................................................. 64 Bilaga B.2 .................................................................................................................................. 67 Bilaga B.3 .................................................................................................................................. 68 Bilaga C.1 .................................................................................................................................. 69 Bilaga C.2 .................................................................................................................................. 70 Bilaga D.1 .................................................................................................................................. 71 Bilaga E.1 .................................................................................................................................. 72 Bilaga F.1................................................................................................................................... 73 Bilaga G.1 .................................................................................................................................. 74 Bilaga H.1 .................................................................................................................................. 75 Bilaga I.1 ................................................................................................................................... 76 Bilaga J.2 ................................................................................................................................... 78 Bilaga J.3 ................................................................................................................................... 79 Bilaga J.4 ................................................................................................................................... 80 Bilaga J.5 ................................................................................................................................... 81 Bilaga K.1 .................................................................................................................................. 83 Bilaga L.1 .................................................................................................................................. 84 Bilaga L.2 .................................................................................................................................. 85 Bilaga L.3 .................................................................................................................................. 86 Bilaga L.4 .................................................................................................................................. 87 Bilaga L.5 .................................................................................................................................. 88 Bilaga L.6 .................................................................................................................................. 89 Bilaga M.1 ................................................................................................................................. 90 Bilaga M.2 ................................................................................................................................. 91 Bilaga O.1 .................................................................................................................................. 92 Bilaga P.1................................................................................................................................... 93.
(9) 1 Inledning I detta kapitel redovisas bakgrunden till examensarbetet samt en närmare beskrivning av problemområdet. Ytterligare redovisas syftet och målen och som avslutande del beskrivs de uppsatta avgränsningar som gjort detta arbete genomförbart.. 1.1 Bakgrund AB Sandviks stora tillverkningsenhet är placerad i Gimo. En av dess enheter tillverkar skärande verktyg. Fabrikslayouten är flödesgrupp och totalt består enheten av nio flödesgrupper vilka är indelade inom tre produktområden (svarvverktyg, fräsverktyg samt borrar). Varje flödesgrupp tillverkar en produktfamilj inom vilken det finns varierande storlekar och utformningar. För några år sedan infördes en ny tillverkningsmetod för svarvbomstillverkning på GVH4. Tillverkningen inom denna flödesgrupp består därför idag av två metoder, en där svarvbommen bearbetas från ett ohärdat stålämne samt en ny metod som innebär användning av en annan stålsort samt att ämnena härdas före vidareförädling. I dagens produktion av svarvbommar förekommer därför båda tillverkningsmetoderna och volymfördelningen är cirka 60 % ny och 40 % gammal metod. Det är dock inte helt klarlagt vilken av metoderna som är mest lönsam. Sammanställda mått saknas även över vilken kvalitetsskillnad som fås på slutprodukten från de två tillverkningsmetoderna.. 1.
(10) 1.2 Syfte & mål Målet för projektet är att fastställa vilken eller vilka kombinationer av tillverkningsmetoderna bearbetning i härdat respektive ohärdat tillstånd, som är mest lämpligt ur ett produktionsekonomiskt samt kvalitetsmässigt perspektiv för Sandvik Coromants tillverkning av svarvbommar. Då avdelningen planerar att byta ut gammal produktionsutrustning skall projektet även skapa underlag som kan användas vid framtida beslut om nyinvesteringar på GVH4. För att uppnå målen för detta projekt skall följande steg utföras. 1. Som grund för arbetet upprättas en nulägesanalys med kartläggning av: • • • • • • •. Dagens produktionsvolymer för respektive produkt och tillverkningsmetod. Layout för flödesgruppen. Flöden för respektive tillverkningsmetod. Produktionsledtider och operationstider. Skillnader mellan metoderna i olika tillverkningssteg. Kostnader för resurser. Kvalitetsaspekter.. 2. Utifrån nulägesanalysen och med stöd av en litteraturstudie bedrivs fortsatt arbete med att: • • • •. Skapa ekonomiska kalkyler som redogör för tillverkningskostnader med respektive tillverkningsmetod. Utreda vilken tillverkningsmetod för de olika produkterna som krävs för att uppnå interna och externa kvalitetskrav. Utreda vilken volymfördelning för respektive tillverkningsmetod som är optimalt ur ett kvalitetsmässigt och ekonomiskt perspektiv. Utreda vilken metod som skall föredras vid nyinvesteringar.. 1.3 Avgränsningar • • • • •. Tillverkningsprocess för respektive metod anses optimal. Utredningen innefattar material från inleverans till slutmontering. Då produktfloran är stor begränsar sig utredningen till utvalda artiklar. Utredningen baserar sig på prognostiserad tillverkningsvolym för år 2008. Utvärdering av kvalitet baseras på befintlig data exempelvis kvalitetskontroll, reklamationer, kassationer osv.. 2.
(11) 2 Företagsbeskrivning I detta kapitel presenteras historia och fakta om Sandvikkoncernen. En kort beskrivning ges över vilken roll Sandvik Coromant har i organisationen. Som avslutande del görs en närmare beskrivning av produkten svarvbom som tillverkas på avdelningen GVH4.. 2.1 Sandvik Sandvik grundades som företag 1862 av Göran Fredrik Göransson. Göransson var den första någonsin att framställa stål enligt Bessemermetoden och det var denna innovation som lade grunderna för företaget. I företagets inledningsskede reste Göransson själv runt för att marknadsföra sina produkter. Hans affärsidé byggde på en direkt kontakt mellan tillverkare och kund och detta är något som fortfarande lever kvar inom företaget. Genom åren har innovationerna inom företaget fortsatt och lett till fram till nya produkter. Redan på 1860-talet fanns borrstål för bergborrning på produktprogrammet. 1921 startades tillverkning av rostfritt stål och 1942 tillverkning av hårdmetall. Under 1950-talet började även hårdmetall att användas för metallbearbetning. Sandviks filosofi är att upprätthålla en ledande ställning inom utvalda områden. Kvaliteten på produkterna är centralt inom verksamheten. Målet är att skapa produkter och service som höjer produktiviteten för kunden. Områden för utveckling ligger inom prestanda, kvalitet, snabbhet, säkerhet, flexibilitet och totalekonomi. Förutom tillväxten inom bolaget har en rad företagsförvärv under 1900-talet gett upphov till den bolagskoncern som Sandvik är idag. I dagsläget har koncernen cirka 47000 anställda och finns representerade i 130 olika länder. Omsättningen är ca 86 miljarder kr. Sandviks affärsområden är koncentrerat inom tre kärnområden. Tooling - Inom affärsområdet Tooling ligger inriktningen på utveckling och tillverkning av verktyg för metallbearbetning. De största kunderna till dessa verktyg är bland annat bil- och flygindustrier. Mining and Construction - Inom detta område har Sandvik inriktat sig på maskiner och verktyg för gruvindustrin. Materials Technology - Inom detta område utvecklas speciallegeringar, rostfria stål samt värmematerial. Kunderna representeras av de flesta industrisegmenten.. 2.1.1 Sandvik Coromant Gimo Sandvik Coromant i Gimo är Sandvikkoncernens huvudenhet för tillverkning av vändskär och verktyg för skärande bearbetning. Anläggningen grundades 1952 och är i dagsläget uppdelad i två fabriker, skärtillverkning (GH) samt verktygstillverkning (GV). Verktygsfabriken tillverkar produkter för olika områden inom skärande bearbetning. Dessa är svarvverktyg, fräsar samt borrar. Skärenheten står för tillverkningen av de skär som kan monteras på verktygen. Vid anläggningen jobbar i dagsläget 1600 anställda. Alla produkter som tillverkas går på export till Sandviks huvudlager i Holland, USA samt Singapore.. 3.
(12) 2.2 Svarvbommen Svarvning är en grundläggande metod inom skärande bearbetning. Med denna metod kan en mängd olika detaljer framställas. En svarv åstadkommer cylindriska former med ett enkelskärigt verktyg. Vid svarvning är den roterande rörelsen förlagd till arbetsstycket medan verktyget i regel är stationärt. Beroende på detaljers utformning krävs att olika svarvmetoder användas. Dessa metoder kräver olika utformning på de verktyg och skär som används. Vid den verktygstillverkande avdelningen i Gimo produceras flertalet produktfamiljer för olika metoder av svarvning. En av dessa produktfamiljer är svarvbommen (se figur 2.1) tillverkas på avdelningen GVH4. Figur 2.1. Svarvbommar Svarvbommar används vid invändig bearbetning av detaljer. Denna bearbetning kräver speciella krav på verktyget. Vid invändig svarvning bearbetas detaljer förberedda med borrade, smidda eller gjutna hål där krav på toleranser samt ytfinhet finns. Vid utvändig svarvning kan verktyg oftast utan problem väljas så att de klarar påfrestningar som uppstår vid bearbetning. Vid invändig svarvning skapar däremot detaljens utformning begränsningar för verktygen. Hålets djup i detaljen som skall bearbetas fodrar ett överhäng hos verktyget. Detta överhäng i förhållande till håldiametern avgör stabiliteten för verktyget. Minskad stabilitet kan leda till att en utböjning av verktyget uppstår på grund av de radiella och tangentiella krafter som inverkar vid bearbetning. Stabiliteten på verktyget är även viktigt för att minska risken för att vibrationer uppstår. Valet av rätt svarvbom vid invändig bearbetning är således viktig. Sandvik Coromant erbjuder ett brett sortiment av svarvbommar till sina kunder. Vid tillverkningen på GVH4 består produktfloran av en mycket stor flora av produkter. Mellan dessa produkter finns olika variationer i diameter, längd samt plattläge. Plattlägets design är viktig för resultatet vid bearbetning och finns därför i många olika utföranden. Skillnader mellan plattlägen finns i fastspänningssystemet för skäret, plattlägets storlek och geometri samt höger- eller vänsterutförande. Vissa svarvbommar förses även med en invändig kanal för att möjliggöra tillförsel av kylvätska vid bearbetning. Kylvätska minskar slitaget på verktygets skär, bidrar till en bättre spånbrytning samt förenklar spåntransporten. Dessa faktorer leder i sin tur till en ökad livslängd för verktyget samt en ökad kvalité på tillverkade detaljerna.. 4.
(13) 3 Nulägesbeskrivning I nulägesbeskrivningen redovisas hur tillverkningen av svarvbommar utförs i dagsläget på GVH4. För att underlätta förståelsen kommer först en översiktlig beskrivning av produktionsupplägget samt artiklarnas flöde att ges. Utöver detta kommer sedan olika delprocesser att beskrivas mera ingående. Även avdelningens informationsflöde kommer att beskrivas.. 3.1 Produktionsupplägg För tillverkning av svarvbommar på GVH4 finns en tilldelad yta på ca 1200 kvm. På denna yta finns samtliga maskiner för bearbetning placerade. Fabrikslayouten som används vid GVH4’s tillverkning är flödesgrupp då samtliga maskiner för bearbetning finns samlade inom en begränsad yta. Flödesgruppen är produktorienterad då endast tillverkning av svarvbommar utförs (se bilaga I.1). Tillverkningen av svarvbommar utförs i dagsläget med två olika metoder. Skillnaden mellan metoderna är att härdning och anlöpning av ämnen sker vid olika tillfällen i tillverkningsprocessen. Metoderna benämns som härdad och ohärdad metod. Materialflödet för dessa metoder är olika vid tillverkningen och benämns som T-120 linjen (ohärdad metod) samt T-121 linjen (härdad metod). Diagram 3.1. Volymsfördelning mellan tillverkningsmetoder på GVH4. Ohärdad metod (T-120) 44%. Härdad metod (T-121) 56%. Den ohärdade tillverkningsmetoden innebär att svarvbommens skaft och plattläge bearbetas innan härdning och anlöpning. Vid tillverkning med den härdade tillverkningsmetoden sker denna bearbetning efter härdning och anlöpning. Tillverkningsprocessen sker i sju delprocesser för den härdade metoden samt åtta delprocesser för den ohärdade metoden. Den extra delprocessen som tillkommer för den ohärdade tillverkningsmetoden är riktning. Detta steg i tillverkningsmetoden krävs då formförändringar uppstår vid härdning och anlöpning. Ett antal produkter som tillverkas med den ohärdade tillverkningsmetoden har ingen kylkanal, detta innebär att tillverkningsprocessen då endast består av 7 delprocesser. Figuren 3.2 nedan visar de tre tillverkningsflödena.. 5.
(14) Figur 3.2. Flöden GVH4 Eftersom de två tillverkningsmetoderna utnyttjar samma maskiner skiljs och möts flöden vid olika delprocesser, detta på grund av de olika ordningsföljderna på tillverkningsstegen i de två linjerna. I dagsläget varierar skiftformerna i flödesgruppen mellan delprocesser då behovet av kapacitet varierar. Kapaciteten begränsas av raster, möten samt planerade och oplanerade stopp. Om extra kapacitet erfordras läggs extra skift in, oftast under nätter eller helger. Bemanningsfaktorn varierar mellan delprocesser, som mest bemannas dock en maskin av en operatör (se bilaga O.1).. 3.1.1 Råmaterial Råmaterial levereras till GVH4 från en underleverantör vid beställning. Vid leverans har råmaterialet dimensioner samt geometrier som möjliggör inspänning i första delprocessen. Dimensioner på råmaterialet varierar beroende på vilken svarvbom som skall tillverkas. Parametrar som påverkar råämnets mått är vilken längd, diameter samt utformning på plattläge som en färdig artikel skall erhålla. Ytterligare utökas råämnesfloran av att ämnen beställs i två olika stålsorter då tillverkningsmetoderna kräver olika material. Råmaterial placeras vid leverans i en inbuffert på GVH4, där väntar ämnena till dess att en order initieras (se bilaga I.1).. 3.1.2 Internlego Tre av delprocesserna vid tillverkningen av svarvbommar utförs inte inom flödesgruppen på GVH4. Dessa utförs istället via internlego. De delprocesser som inte utförs inom flödesgruppen är härdning, anlöpning, Jettalisering samt märkning med logotyp. Till internlegoavdelningen skickas produkter från flera avdelningar på fabriken. Delprocesserna i internlegoavdelningen är belagd med en överkapacitet för att mellanlager inte skall uppstå. Genomloppstider i dessa delprocesser kan dock variera om material från flera olika avdelningar anländer inom en begränsad tidsperiod, alternativt att problem uppstår på avdelningen. Avdelningar som skickar artiklar till internlegoavdelningen debiteras för dessa via en interndebitering.. 3.1.3 Materialhantering Materialhantering mellan delprocesserna vid tillverkning kan delas upp i två kategorier, transporter inom flödesgruppen samt transporter till och från internlegoavdelningen.. 6.
(15) Hantering av material inom flödesgruppen sker med speciella vagnar som finns tillgängliga i produktionen, alternativt med EU-pallar. Vagnarna som är konstruerade efter svarvbommarnas dimensioner samt vikt används av operatörerna för att förflytta materialet mellan delprocesserna. Detta utförs manuellt av operatörerna. Mellan vissa delprocesser används även EU-pallar för att förflytta material. Vid förflyttning av dessa används en truck som finns tillgänglig inom flödesgruppen. För hantering av material mellan flödesgruppen och internlegoavdelningen används de vagnar som finns tillgängliga i produktionen. Vid de delprocesser inom flödesgruppen som efterföljs av internlegotillverkning finns speciella platser för avhämtning. Dessa är placerade längs truckgången inom GVH4. Inom verktygstillverkande fabriken (GV) finns truckar för materialtransport till och från internlegoavdelningen. Dessa passerar kontinuerligt avhämtningsplatser och kontrollerar om material skall förflyttas. Efter transport från internlegoavdelningen lämnas material på bestämda platser intill den efterföljande delprocessen.. 3.2 Delprocesser 3.2.1 Pipborrning (BKH) I flödesgruppen finns en automatiserad pipborrmaskin (se bilaga I.1). I denna maskin borras en kylkanal genom ämnet vilket möjliggör tillförsel av kylvätska vid användning av svarvbommen. För denna operation finns ett flertal olika diametrar på de borrar som används, detta beroende på vilken produkt som tillverkas. Eftersom denna delprocess är placerad före härdning och anlöpning i de båda tillverkningsmetoderna utförs endast bearbetning i ohärdat material. Detta innebär att ingen skillnad finns i operationstider mellan de olika tillverkningsmetoderna. Vid bearbetning i pipborrmaskinen laddas material manuellt i palletter av operatören, från vilka automatisk laddning i maskinen sedan sker med en integrerad robot. Maskinen bearbetar tre arbetsstycken samtidigt. Under bearbetning laddas tre obearbetade arbetsstycken från paletter till en fixtur av roboten. När bearbetningen är klar placeras de tre färdigbearbetade arbetstyckena på fixturen varefter de obearbetade placeras i läge för bearbetning. De färdigbearbetade arbetstyckena transporteras sedan tillbaka till paletten från fixturen av roboten.. 3.2.2 Svarvning komplett (SKPL) I flödesgruppen finns två automatiserade fleroperationsmaskiner med kombinerad svarv och fräs. (se bilaga I.1). Material laddas vid denna station i paletter av operatören. Paletterna placeras i maskinen vilken automatiskt laddar svarven från dessa med en transportör. Transportören är utrustad med två gripklor som används för att hantera materialet. I svarvdelen bearbetas ämnet för bommen till i det närmaste färdig tolerans för bommens skaft, den del som sedan skall fräsas till plattläge grovbearbetas. Olika mängd material lämnas vid grovbearbetningen, detta beroende på om bommen skall bearbetas före eller efter härdning. Skillnaden i den materialmängd som lämnas, kommer av att bommar i den ohärdade metoden kräver extra slipmån efter riktningen för att erhålla rätt toleranser. När ämnet är färdigbearbetat i svarvdelen förflyttas det av transportören till fräsdelen.. 7.
(16) I fräsdelen planas tre ytor på bommens skaft till färdiga mått. Efter att bearbetningen är utförd i fräsen placeras bommen åter på palleter av transportören. Allt eftersom palleter fyllts med artiklar plockas de ut ur maskinen av operatören. Artiklarna lastas sedan manuellt till eu-pallar eller vagnar och förs till nästa delprocess. Bearbetning i härdat material kräver andra skärdata än vid bearbetning i ohärdat material. Matning, varvtal samt skärdjup är lägre vid bearbetning i härdat material. Cykeltiderna blir därför längre än vid bearbetning i härdat material. Vid bearbetning i ett härdat material i svarvdelen krävs andra skär än vid bearbetning i ohärdat material. Detta eftersom ingreppet i härdat materialet är mer påfrestande. Även då andra skär används vid bearbetning med härdad metod är livslängden högre hos skär i den ohärdade metoden. I SKPL finns parametrar i NC-programmen för fräs- och svarvdelen som registrerar när skär är utslitna. I svarvdelen anger parametrarna hur många ämnen som kan tillverkas med varje grov- samt finskärsegg. Antalet bitar som kan tillverkas varierar med mängden material som skall avverkas. I fräsdelen anger parametrarna hur lång ingreppstid varje skäregg klarar för respektive metod. Då matningen är högre vid ohärdad bearbetningsmetod blir ingreppstiden lägre per artikel än vid bearbetning i liknande artiklar för härdad metod. Detta i kombination med lägre slitage innebär att skär håller längre vid bearbetning i ohärdat material. När maskinen registrerar att skär är utslitna stannar den och larmar. Dessa skär måste då vändas eller bytas ut av operatören. Efter varje byte eller vändning av skär måste maskinen stoppas efter bearbetning av första artikeln. Detta för att kontrollera att rätt mått erhålls. Om måtten ändrats måste en korrigering utföras i NC-programmet. Detta moment kan ibland ge upphov till att maskinen står stilla om det inträffar i samband med att operatören inte finns tillgänglig vid maskinen.. 3.2.3 Fräsning komplett (FKPL) I denna delprocess bearbetas svarvbommens plattläge till färdigtolerans. Detta utförs genom att den del för plattläget som grovbearbetats i SKPL genomgår fräsning, borrning, gängning samt för vissa artiklar även gradning. Eftersom variationerna i utformning av plattlägen är många, skiljer sig antal operationer, bearbetningstid samt cykeltid åt mellan produkterna i denna delprocess. Inom flödesgruppen finns sex stycken nc-styrda fräsar som kan utföra tillverkningssteget (se bilaga I.1). Fyra av dessa är av samma typ och finns placerade i två robotceller (Stamaceller). Dessa robotceller är utformade så att manuellt laddade palletter tillförs, från vilka en robot sedan laddar de båda fräsarna med arbetsstycken. I dessa finns möjligheter att ladda flertalet olika ordrar samt artiklar samtidigt i cellen. De två ytterligare fräsarna (Hermle- samt Matsuurafräs) är fristående. I dessa placeras artiklar i palletter av operatören från vilket maskinen sedan laddas automatsikt. Matsurafräsen är en gammal maskin som är på väg att avvecklas, i denna maskin bearbetas endast bommar där NC-program inte blivit anpassade till de nyare maskinerna (Hermle samt Stama). Vid bearbetning av bommarnas plattlägen i FKPL uppstår grader på de ställen där avverkat material inte bryts loss ordentligt. Problem med grader skiljer sig åt mellan bommarna beroende på materialens egenskaper. Vid bearbetning i härdat material bryts graderna lättare bort än vid bearbetning i ohärdat material. Grader som finns kvar på bommen efter det att bearbetningen avslutats är ett problem. Dessa grader måste avlägsnas manuellt av operatörer genom att. 8.
(17) operatörerna manuellt filar och borstar arbetsstyckena. Kvaliteten på bommen kan påverkas negativt av detta manuella ingrepp, då toleranser för ytor, kanter och hål påverkas. För tillfället utvecklar emellertid Sandvik Coromant en ny konceptuell metod för bearbetning, denna metod gör det möjligt att bearbeta till ett gradfritt resultat. I NC-programmen för fräsarna finns en funktion som mäter de olika verktygens totala ingreppstid. Varje verktyg har en parameter som anger ingreppstid innan det är utslitet. När ett verktyg är utslitet växlas ett nytt in från fräsarnas verktygsmagasin. Operatörerna byter sedan ut dessa utslitna verktyg från magasinen. Bearbetning i härdat material kräver lägre matningar, andra skärdjup samt andra spindelvarvtal än vid ohärdad bearbetning. Detta betyder att cykeltider för fräsen ökar vid bearbetning i härdat material. För bearbetning i härdat respektive ohärdad metod används idag samma typ av verktyg och skär. De parametrar som registrerar när ett verktyg är utslitet har samma värde vid bearbetning i de två materialtillstånden. Bearbetning i härdat tillstånd sliter dock mer på verktyg än bearbetning i ohärdat tillstånd. Detta i kombination med att samma verktyg, skär och parametrar används, leder till att verktyg vid ohärdad tillverkningsmetod ibland byts trotts att dessa inte är utslitna. Operatörerna kontrollerar med jämna mellanrum om utslitna verktyg finns i fräsarna. Programmet för varje fräs visar vilka verktyg som är utslitna eller snart blir utslitna. För varje verktyg finns minst ett reservverktyg i ett sekundärverktygsmagasin. För de verktyg som har lång ingreppstid per detalj finns fler. Ett exempel är planfräsarna, där finns 3-4 reservverktyg i det sekundära verktygsmagasinet. Tiderna för att byta ut ett verktyg varierar. Planfräsar tar i regel längst tid då de kräver inmätning. Längsta tiden för att byta ett verktyg är ca 5 minuter emedan en del bara kräver ca 1 minuts arbetsinsats. Verktygsåtgången per skift varierar beroende på härdad eller ohärdad bearbetningsmetod. Enligt operatörerna vid Stamacellerna byts högst 10 verktyg ut under ett skift som pågår 8,5 timmar.. 3.2.4 Slipning (SLR) I denna delprocess slipas infästningsytorna på svarvbommen till färdigtolerans. Dessa ytor används sedan vid infästning när svarvbommen skall användas, det är därför viktigt att rätt toleranser erhålls. I flödesgruppen finns två stycken maskiner för slipning (se bilaga I.1). Den ”modernare” av maskinerna laddar artiklar automatiskt med en integrerad robot. Detta sker från paletter som laddas manuellt av operatörer. I den äldre slipmaskinen krävs manuell laddning av en operatör inför bearbetning av varje artikel. Denna maskin är emellertid planerad att ersättas av en ny. Vanligtvis används denna äldre maskin till att bearbeta artiklar med större diameter än 32mm samt ordrar med små volymer. I den nyare slipmaskinen omsluter två mätarmar svarvbommens skaft under bearbetning, detta för att kontrollera hur mycket material som skall avverkas. Eftersom slipningens utförande styrs av mätarmarna och inte ett identiskt program för varje produkt förekommer variationer i cykeltider för en och samma produkt. Den äldre slipmaskinen styrs av ett NC-program. Detta innebär att cykeltider blir identiska. Här är det operatören som ställer in hur maskinen skall slipa. Detta gör att cykeltiden även beror av vilka inställningar som operatören har gjort, exempelvis hur stor säkerhetsmån som används vid ingången till arbetsstycket.. 9.
(18) Livslängden hos de slipskivor som används varierar. Med jämna mellanrum skärps slipskivorna för att rätt toleranser hos arbetsstyckena skall erhållas. Slipskivorna används så länge de kan prestera de rätta toleranserna.. 3.2.5 Riktning av svarvbommar (RK) De artiklar som tillverkas med ohärdad metod kräver riktning för att erhålla rätt toleranser. Vid härdning och anlöpning av artiklar uppstår formförändringar, dessa går inte att kompensera för i förväg. Denna förändring åtgärdas i delprocessen riktning. I flödesgruppen finns en maskin för riktning av svarvbommar (se bilaga I.1). Denna sköts manuellt av en operatör som först kontrollerar vilka formförändringar som uppstått på bommens skaft i härdning, detta med ett mätinstrument. Om en förändring skett måste bommen riktas tills det kompenserats för denna. Detta görs genom att en artikel först placeras i riktmaskinen. Sedan aktiveras en hydraulcylinder av operatören som applicerar en kraft mot svarvbommens skaft varpå en krökning uppstår. Detta förfarande upprepas tills det att svarvbommen erhåller rätt toleranser för nästföljande delprocess, slipning.. 3.2.6 Härdning och anlöpning (HÄ+ANL) Härdning och anlöpning utförs på internlegoavdelningen. Detta steg i tillverkningen sker i flera delmoment. Artiklar placeras först på en härdfixtur. Detta görs manuellt av operatörer. Fixturen förs sedan till första delmomentet som är förvärmning. Här förvärms ämnena. Efter detta transporteras fixturen med ämnena till härdning. Där hettas först ämnena upp till en specifik temperatur som gör att stålet når sitt austenitområde. När stålet når rätt temperatur får det tillbringa en fastställd tid i härdugnen. Efter detta kyls ämnena med olja. När detta utförs ökar hårdheten hos stålet. Efter avkylningen får ämnen fortsätta att svalna under en fläkt. Nästkommande moment är tvättning, detta utförs för att avlägsna den olja som använts vid kylningen. Då artiklarna rengjorts går de vidare till anlöpning. Här hettas ämnena upp till en specifik temperatur, denna hålls sedan konstant under en bestämd tid. Vid anlöpningen ökas stålets seghet och inre spänningar från härdningen frigörs. Till sist får ämnena svalna varefter operatörer tömmer härdfixturerna. Härdning och anlöpning tar 8 timmar från det att ämnena påbörjar förvärmning tills dess att de kan plockas från fixturerna. Vid härdning och anlöpning finns ingen tidsskillnad för behandlingen i processen mellan de olika stålsorterna. Den skillnad som finns ligger i ugnarnas kapacitet. Då ämnena för den härdade tillverkningsmetoden inte har bearbetats förutom i BKH väger dessa mer än de som går i den ohärdade. Detta leder till att fler ämnen kan härdas samtidigt för den ohärdade tillverkningsmetoden.. Figur 3.3. Flöde internlegoavdelning. 10.
(19) 3.2.7 Ytbehandling och montering av logotyp (JET+KLISKY) För att erhålla ett skydd mot korrosion samt för att få ett estetiskt tilltalande utseende passerar svarvbommarna som ett steg i tillverkningen en Jettalisering (JET). Denna delprocess brukar även benämnas, svartoxidering eftersom den skapar en svart oxid på ytan av svarvbommarna. Ytbehandlingen utförs i ett antal steg där bommarna först rengörs grundligt. Detta påbörjas genom att svarvbommarna fästs på speciella galgar som sedan placeras vid Jettaliseringen. Behandlingen inleds med att en transportör tar galgen med svarvbommarna och sänker ned den i ett flertal rengöringsbad. Antalet rengöringsbad varierar beroende på om bommarna går i T-120 respektive T-121 linjen. Bommar i T-120 linjen går direkt från härdningen till jettaliseringen och är på grund av detta kraftigt smutsade från föregående härdoperation, detta leder till att ett större antal rengöringsbad måste användas. Som sista steg i denna rengöringsprocess passerar svarvbommarna en ultraljudstvätt. Efter rengöring sänks svarvbommarna ned i en svartoxidlösning. Denna reagerar med svarvbommarnas yta och de genomgår en kontrollerad oxidering. Slutligen transporteras svarvbommarna tillbaka till startpunkten för processen. Jettaliseringsprocessen varierar i utförande mellan de olika tillverkningsmetoderna, då hårdheten i materialet gör att bommarna reagerar olika med oxiden samt att artiklar härdade som tillverkningssteg innan jettaliseringen måste rengöras mera utförligt. Delprocessen tar på grund av dessa skillnader olika tid i de två T-linjerna. Efter Jettaliseringen placeras svarvbommarna på vagnar och förflyttas till en maskin som märker dem med en klisterlapp (KLISKY). För att tydliggöra att Sandvik Coromant tillverkat produkten klistras Sandviks logotyp fast längs svarvbommens sida. Detta sker automatiskt i en maskin som kan laddas med flertalet artiklar samtidigt. Efter detta placeras åter svarvbommarna på vagnar och transporteras till nästa delprocess.. 3.2.8 Montering och avsyning (M+ASY) Sista steget för produkter som passerar flödesgruppen är montering och avsyning (se bilaga I.1). Där monteras den fästanordning som håller skäret i plattläget vid bearbetning. Denna fästanordning varierar mellan de olika produktgrupperna av bommar. Monteringens utförande och tiden för detta skiljer sig därför åt. All montering utförs manuellt av operatörer. Som avslutande steg sker en avsyning.. 3.3 Informationsflöde 3.3.1 Orderhantering De produkter som tillverkas av GVH4 distribueras till Sandvik Coromants lager i Holland och USA. Lagren använder sig av beställningspunktsystem för materialplanering, dvs. när lagersaldot sjunkigt till beställningspunkten, genereras en order. Beställningspunkt och orderstorlek för en produkt bestäms av den prognostiserade efterfrågan. En Produkt med hög omsättning har således en beställningspunkt vid ett högre lagersaldo samt en större orderstorlek än en produkt med låg omsättning. Lagersaldon uppdateras veckovis och ordrar inkommer då på produkter som måste tillverkas. Om brist uppstår på en produkt där ledtiden från beställning till leverans är nära efterfrågan under samma period, prioriteras ordern för denna produkt. Ordrar som planeras tilldelas en prioritet utifrån hur akut behovet är. Ordern märks med prio 10, 20, 30, 40 eller 50. Ordrarna skickas automatiskt via Sandviks interna data system (IMS) till avdelningens materialplanering. Materialplanering sköts av produktionsledaren i samarbete med operatörerna. 11.
(20) Övervakningen av startade order i produktionen har ingen elektronisk loggning. Detta medför att startade order manuellt måste uppsökas för att kontrollera vart i produktionen de ligger. Detta är problematiskt och påbörjade ordrar kan ibland vara svåra att finna ute i produktionen.. 3.3.2 Orderstart Via IMS tilldelas ordrar för de produkter som skall tillverkas till operatörerna vid första delprocessen (BKH och SKPL). Före en order kan startas måste råmaterial beställas. Detta utförs av operatören som via ett datorsystem skickar en beställning till underleverantör. Tiden från beställning till leverans varierar, en bestämd metod används därför för att alltid ha rätt material tillhanda vid rätt tidpunkt. Operatören är den som bestämmer när en order skall startas i produktionen. Operatörerna vid de första delprocesserna skall kontrollera nivån i mellanlagren för efterföljande steg i produktionen. En ny order startas när det anses lämpligt, såvida den inte har hög prioritet. Ordrar med högsta prioritet startas alltid fortast möjligt. Ordrar som startas tidigare med lägre prioritet tas då åt sidan för att försöka minska genomloppstiden i produktionen för prioriterade ordrar. Vid ett normalt förfaringssätt väljer operatören ordrar från IMS som har högsta prioritet. Vanligt är att ordrar med samma dimensioner i SKPL och BKH slås samman och bearbetas samtidigt, detta för att minska antalet omställningar. När en order startas skriver operatören ut en orderhandling som skickas med materialet. Materialplaneringen på GVH4 övervakar dagligen de ordrar som startats. Om prioriteten för en order ändras i IMS under genomloppstiden i tillverkning, måste ordern sökas upp i produktionen och prioriteten förändras. Som tidigare nämnts kan ordrar vara svåra att hitta på grund av att de inte registreras i tillverkningsstegen.. 3.3.3 Produktionen Den orderhandling som skrivs ut vid en orderstart följer med svarvbommarna genom samtliga delprocesser. Orderhandlingen läggs på den vagn eller EU-pall som materialet transporteras med. I varje order finns ritningar och information som krävs för att samtliga delprocesser skall vara möjliga att utföra samt information om vilket nästkommande delprocess i tillverkningen är. Efter varje delprocess antecknas i orderhandlingen hur många godkända bitar som tillverkats. Uppgifter om antal bitar av råmaterial som togs ur lager antecknas och vid varje delprocess fylls även i om några kassationer uppstått. Anledningen till eventuella kassationer fylls i med en kod. Denna kod beskriver vilken maskin, anledning till kassaktion, tillverkningsmetod samt hur många bitar som kasserats.. 12.
(21) 4 Teoretisk referensram I detta kapitel beskrivs den teoretiska referensram som detta examensarbete baseras på och som sedan legat till grund när problemområdet behandlats. Första delen av kapitlet fokuserar på produktionsekonomi. Här behandlas några av de aspekter som kan anses värdefulla att beaktas i dagens tillverkande industri. Nästa del i kapitlet fokuserar på ekonomiska kalkyler. Här beskrivs påläggskalkyl och aktivitetsbaserad kalkyl. Som avslutande del presenteras verktyget värdeflödesanalys som använts för att göra en grundlig kartläggning av flödena på GVH4.. 4.1 Produktionsekonomi På dagens konkurrenskraftiga marknad har tillverkande industriföretag fått allt svårare att bibehålla lönsamhet genom höga priser. Lönsamhet måste istället uppnås genom låga tillverkningskostnader, god produktkvalité, korta genomloppstider samt ständig produktutveckling (Skärteknik, 2005). Enligt Ohlhager (2000) är de mål som eftersträvas inom produktionsekonomin lönsamhet, kvalitet, flexibilitet, leveransförmåga samt produktivitet. Dessa faktorer är många gånger motstridiga och oftast beroende av varandra. Att tillverka en eftertraktad produkt med en god och jämn kvalité, kräver oftast en omfattande insatts av kapital samt arbete. För att uppnå en god produktionsekonomi med bra lönsamhet bör därför en bra balans uppnås mellan (Hågeryd, Björklund och Lener 2002). . Produktionskostnad Produktionskvalité Produktionstid. 4.1.1 Produktkostnad När en produkt skall tillverkas uppstår flertalet kostnader. För att uppnå lönsamhet måste dessa kostnader täckas av intäkter från försäljning. Helst skall skillnaden mellan intäkterna och kostnader skapa en vinst. Målet med produktionsekonomin är att förädla en produkt så att den slutgiltiga produkten har ett högre värde för kunden än summan av de insatsresurser som lagts ned på denna (Olhager, 2000). Kostnader för insatsresurserna vid tillverkning av produkter inom industrin varierar med produkten. De vanligaste kostnader som uppstår i de flesta tillverkande företag kan sammanfattas som. Lokalkostnad - För att tillverka en produkt krävs en lokal, för denna uppstår oftast kostnader för bundet kapital, värme, el underhåll etc. Maskinkostnad - För att tillverka en produkt krävs maskiner. Dessa måste först köpas in, sedan kräver de en installation, underhåll samt reparationer. Kostnaderna för dessa maskiner är kapitalbindning, avskrivningar underhåll- och reparationskostnader etc. Operatörskostnad - För att tillverka produkter krävs att maskinerna hanteras av operatörer. Kostnader för operatörer är lönekostnader, sociala avgifter etc.. 13.
(22) Verktyg kostnad - Vid tillverkning förbrukas verktyg i maskiner. Kostnader som kan härledas till dessa är, direkt verktygskostnad, kostnad för inköpsfunktion, underhållkostnader, förrådskostnad etc. Kostnader innan tillverkning - Innan en produkt kan påbörja tillverkning krävs oftast ett omfattande arbete i form utav konstruktion, beredning samt programmering. Kostnader för dessa funktioner uppstår då utrustning måste köpas in (avskrivningar och kapitalbindning), löner och sociala avgifter måste betalas etc. Kostnad för råmaterial och kapitalbindning - För att tillverka en produkt krävs råmaterial. Vid tillverkning av en produkt uppstår kostnader vid samma tillfälle som råmaterial köps in. För varje delprocess som produkten passerar och vidareförädlas i, ökar den investerade kostnaden. Det kapital som investeras i produkten återvänder inte till tillverkaren förrän produkter är sålda och kunden har betalat (Skärteknik, 2005). Inom tillverkningsindustrin binds ofta stora kapitalmängder i material som lagerhålls, PIA samt färdigvarulager. Att sträva efter korta genomloppstider i produktionen är något som har blivit allt viktigare, då tiden från att kapital investerades tills det återbetalas minskar. Kostnad för kapitalbindning uppstår främst av kapitalkostnaden, dvs finansieringen för inköpet av insatsvaror. Övriga kostnader som uppstår är för lagerytor, materialhanteringsutrustning, personal, försäkringar för produkter samt inkurans etc. (Olhager, 2000).. 4.1.2 Produktionskvalité Kvalité är ett begrepp med många innebörder. Inom tillverkande företag används ofta detta begrepp som definition för både produkter och produktionsprocesser. Kvalité för en produkt kan på ett förenklat sätt beskrivas som produkters förmåga att uppfylla kunders förväntningar och krav. Inom produktionsprocessen kan kvalité definieras som förmågan att vid maskinbearbetning tillverka produkter med rätt toleranser och dimensioner (Olhager 2000). Kvalitetsdimensioner • • • • • • • •. Prestanda Funktionalitet Tillförlitlighet Överstämmelse med specifikation Hållbarhet Underhållbarhet Estetik Upplevd kvalitet. 4.1.3 Bearbetningskostnad I dagens tillverkande företag är kostnader för bearbetningsutrustning betydande och tim ostnader vid tillverkning därför höga. Dessa faktorer betyder att det är av väsentlig betydelse att maskiner utnyttjas rationellt. För att erhålla en optimal bearbetningskostnad måste hänsyn tas till ett flertal faktorer. Personal, verktyg, utrustning, bearbetningsmetod samt arbetstyckets utformning anses. 14.
(23) vara de viktigaste faktorerna (figur 4.1 illustrera parametrar som kan beaktas för optimal bearbetning). Den leveranstid som önskas av kunden måste även tas hänsyn till. Den bästa kombination av dessa faktorer ger en optimal bearbetningskostnad (Hågeryd, Björklund och Lener 2002).. Figur 4.1. Faktorer för optimal bearbetning. 4.1.4 Maskinutnyttjandegrad Då maskintimkostnaderna oftast är höga är det av stor vikt att maskiner i tillverkningen utnyttjas effektivt. Inom bearbetningsekonomi kan effektivitet inom ett företag delas upp i två delar, yttre effektivitet som syftar att tillverka rätt produkter som sedan kan säljas på marknaden. Den andra är inre effektivitet som syftar till att tillverka produkter till en låg kostnad (Olhager, 2000). För att uppnå en god inre effektivitet måste utnyttjandegraden av maskiner vara hög. Hög nyttjandegrad av maskiner betyder oftast en god bearbetningsekonomi. Undersökningar som utförts visar att NC-styrda maskiner inom tillverkande industrier endast använder 30 % av tiden till effektiv bearbetning. Övrig tid upptas t ex av stillestånd i väntan på arbete, stillestånd pga sjukfrånvaro, ställarbete, driftstörningar samt mätningar. Om maskiner kan utnyttjas effektivare är de områden som påverkas positivt. • • •. Lönekostnader per produkt minskar. Kapitalkostnad för maskiner och annan utrustning minskar per produkt. Genomloppstiderna minskar, vilket minskar kapitalbindningen för produkter i arbete (PIA).. Det är således av stor vikt att med ständiga förbättringar alltid arbeta mot ett mer effektivt maskinutnyttjande. För att förbättra maskinutnyttjandet finns två åtgärder, höja effektiviteten under befintlig drifttid eller att utöka drifttiden. För att höja effektiviteten under befintlig drifttid finns flera åtgärder(Skärteknik, 2005) . •. Organisatoriska förbättringar. 15.
(24) • •. Högre avverkningshastighet. Ökning av driftsäkerheten.. 4.2 Produktkalkylering I dagens konkurrensutsatta miljö behöver beslutsfattare noggrann information över hur produktmix, produktdesign och processteknologi påverkar företagets lönsamhet. Denna information kan anskaffas genom lönsamhetsmodeller som visar samband mellan förtjänst som uppkommer vid försäljning av individuella varor mot den kostnad för resurser som krävs för att designa, producera och sälja dessa produkter (Cooper & Kaplan, 1991). Sedan slutet av 80-talet har det emellertid enligt Gerding pågått en debatt gällande de traditionella kalkylmodellerna. Påläggskalkyleringen som förekommer hos ett flertal av Sveriges industriföretag, har fått kritik för att den inte har utvecklats i förhållande till företagens interna och externa miljö. Sedan den tid då kalkylmodellerna konstruerades vid 1900-talets början har förutsättningarna som kalkylerna baserar sig på kraftigt förändrats, detta medför därför att kalkylanvändare riskerar att fatta felaktiga beslut då kalkylerna appliceras på dagens miljöer (Jonas Gerding, 1995).. 4.2.1 Kalkylernas förutsättningar Den förändring som skett hos industriföretag sedan det förra seklets mitt är omfattande. Det anses svårt att göra någon generell beskrivning av de förändringar som skett då dessa skiljer sig åt avsevärt beroende på vilken bransch som avses. Det kan emellertid gemensamt för de flesta branscher konstateras att marknads och teknologiutvecklingen är två faktorer som kraftigt påverkat produktkalkyleringen.. 4.2.2 Marknadsfaktorer En marknadsfaktor som kraftigt påverkar produktkalkyleringen är den efterfrågan på större produktdifferentiering som uppstått. Produktdifferentiering och kundanpassning är även ett svar från västerländska företag på den konkurrens som vuxit fram från låglöneländer. Produkters livslängd har även minskat, detta i takt med att vikten av att vara först ut på marknaden med nya produkter har ökat. För att skapa förutsättningar att komma först ut på marknaden måste dagens industrier korta sina genomloppstider från idé till färdig produkt. Ytterligare skäl till kravet på allt kortare ledtider är påverkan på kapitalbindningen som i förlängningen påverkar räntekostnader och följaktligen produktpris. Det räcker inte likaså att vara först ut på marknaden och producera till låga priser, att producera med en jämn och hög kvalitet är idag högst väsentligt. Enligt Gerding var det under 50- och 60talet priset som var den dominerande konkurrensfaktorn, på senare år har dock kvalités aspekter blivit allt mer avgörande. Under 70- och 80-talet ökade därav den andel företag som konkurrerade med en kombination av de två faktorerna. Japanska företag låg framförallt i framkant vad gäller denna utveckling (Jonas Gerding, 1995).. 4.2.3 Teknologins förändring Då traditionella kalkylmodeller utformades kännetecknades industrins teknologi av en arbetsintensiv tillverkningsprocess. Sedan slutet av 70-talet har emellertid industrin utvecklats. 16.
Figure
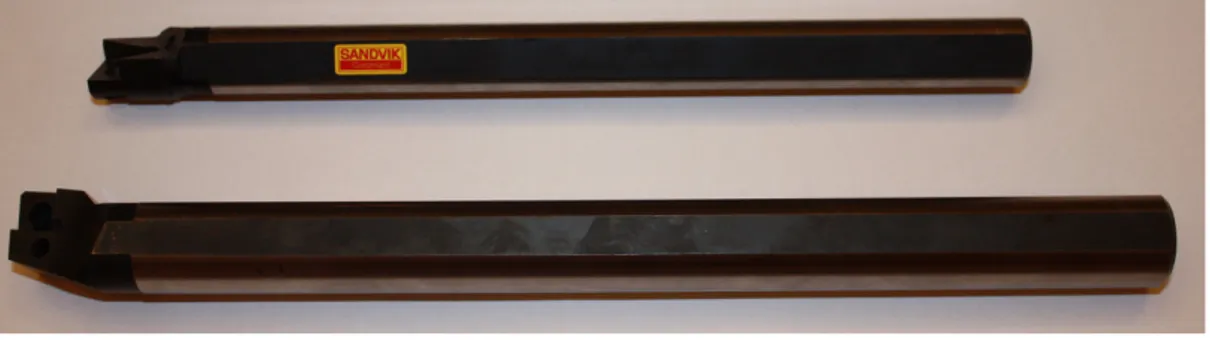
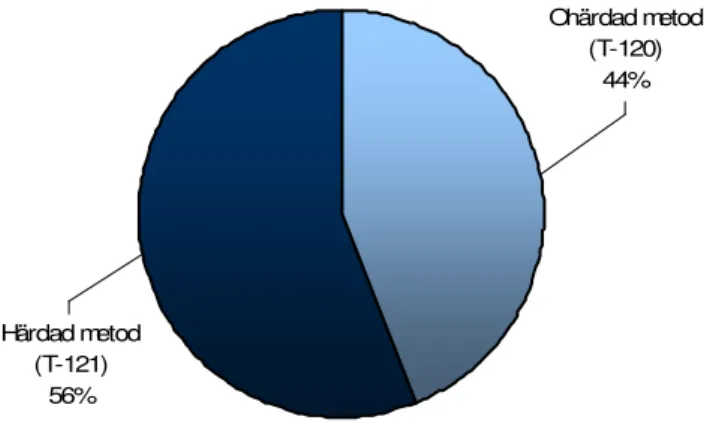

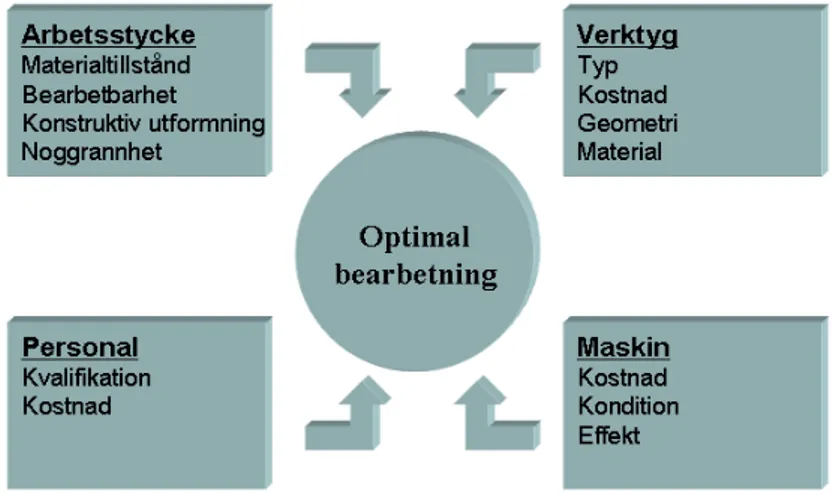
Related documents
En student som blir arbetslös efter examen får leva på sparade pengar, släktingar eller ekonomiskt bistånd. När allt fler väljer att studera vidare krävs det
Myndigheternas individuella analyser ska senast den 31 oktober 2019 redovi- sas till Regeringskansliet (Socialdepartementet för Forte, Utbildningsdeparte- mentet för Rymdstyrelsen
ökade medel för att utöka satsningarna på pilot och systemdemonstrationer för energiomställningen. Många lösningar som krävs för ett hållbart energisystem finns i dag
Vatten är en förutsättning för ett hållbart jordbruk inom mål 2 Ingen hunger, för en hållbar energiproduktion inom mål 7 Hållbar energi för alla, och för att uppnå
Avslutningsvis presenterar vi i avsnitt 6 förslag på satsningar som Forte bedömer vara särskilt angelägna för att svensk forskning effektivt ska kunna bidra till omställningen till
största vikt för både innovation och tillväxt, samt nationell och global hållbar utveckling, där riktade forskningsanslag skulle kunna leda till etablerandet av
Processer för att formulera sådana mål är av stor betydelse för att engagera och mobilisera olika aktörer mot gemensamma mål, vilket har stor potential att stärka
1(1) Remissvar 2021-01-22 Kommunledning Nykvarns kommun Christer Ekenstedt Utredare Telefon 08 555 010 97 christer.ekenstedt.lejon@nykvarn.se Justitiedepartementet